1-Products Name: Resistance Welding Copper Contact Cap for EV Fuse
2-Base Material:
(1) Red Copper Stamping Parts: 99.99% Copper T2Y2(SECu/C1100), %IACS≥97, HV: 80~110s;
(2) Brass Stamping Parts: 65% Brass H65 (CuZn36/C2700), tensile strengthσb MPa≥440
3-Surface Treatments:
(1) Silver plating
(2) Bright tin plating
(3) Lead-free fog tin plating
(4) Nickel plating
(5) Ultrasonic cleaning
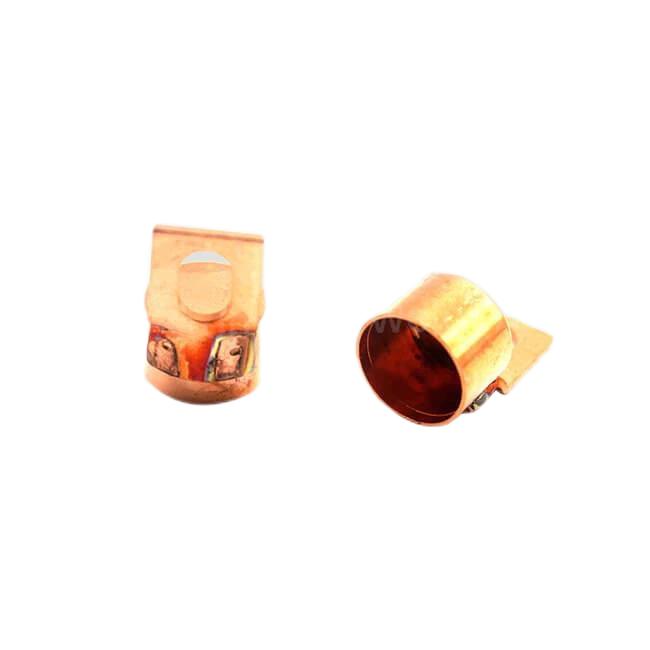
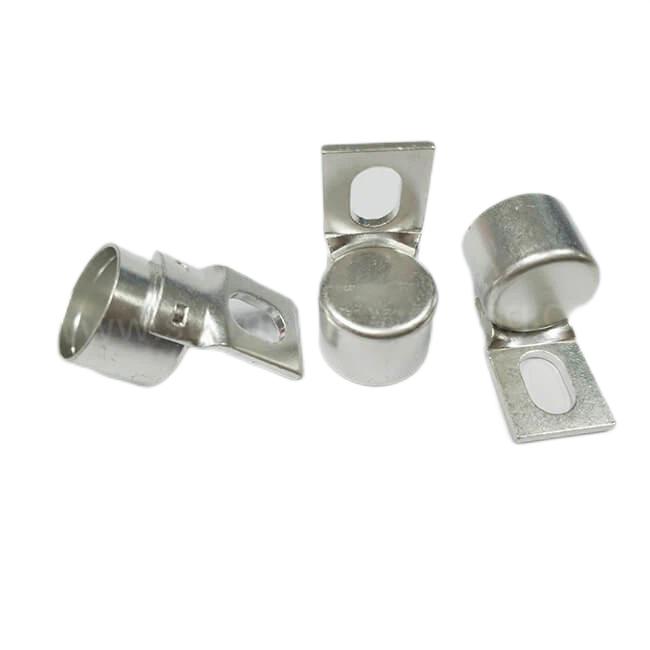
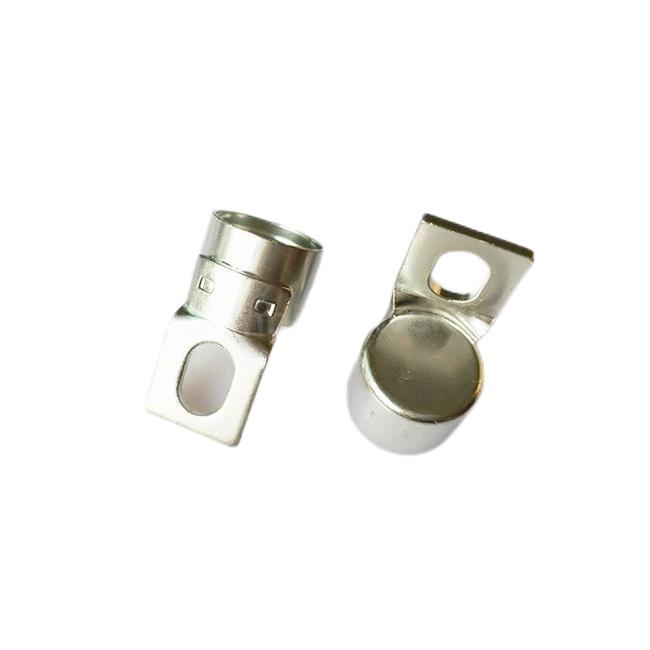
4-Technology Processes:
(1) Stamping
(2) Stretching
(3) Riveting
(4) Plating
(5) Tin Brazing
(6) Silver Brazing
(7) Laser Welding
(8) Resistance Welding
5-Free Samples: 10-50pcs is allowed
6-Lead Time: Orders 7-10days, Samples 20-25days (including the tooling/die production of Copper Stamped Part);
7-Packing: Plastic inside and carton/pallet outside
8-Certifications: ISO9001, IATF16949, RoHS, REACH, etc.
9-Production Capacity: 50,000,000 pcs/month
10-Applications: PV Fuse, EV Fuse, PDU Fuse, Energy Storage Fuse, UPS DC Links, NH Fuse, BS Fuse, Fast Fuse, etc.
Application of Resistance Spot Welding in New Energy Vehicle Fuses
Resistance spot welding is a commonly used metal joining process, particularly suitable for the production of new energy vehicle fuses. This article will focus on the working principle of resistance spot welding, its production process in fuse manufacturing, advantages, and its application in new energy vehicles.
1- Principle of Resistance Spot Welding:
Resistance spot welding utilizes the heat generated by the current passing through the workpieces to melt and join them. In fuse production, it is commonly used to connect components such as Fuse Copper Contact, Fuse Copper Cap, Terminal Contact, and Fuse Terminal.
2- Production Process of Resistance Spot Welding:
(2.1) Preparation:
Prepare welding equipment, including welding machine, electrodes, and current control system.
Prepare welding materials, typically solder or other suitable welding materials.
(2.2) Surface Treatment:
Clean and treat the surfaces of the welding parts to ensure they are free of oil, oxide, and other impurities.
Position and fix the parts to be welded for subsequent welding operations.
(2.3) Welding Operation:
Place the welding parts in the appropriate position to ensure the current can flow through the desired connection points.
Heat the welding parts with current to melt them locally and form welding joints.
Control the welding time and current intensity to ensure welding quality and stability.
(2.4) Quality Inspection:
Inspect the appearance and welding quality of the completed parts to ensure the welding joints are firm and reliable.
Advantages of Resistance Spot Welding:
High efficiency: Resistance spot welding process is fast, significantly improving production efficiency.
Good welding quality: Resistance spot welding joints are strong and reliable, resistant to loosening or fracture.
High degree of automation: Resistance spot welding can be combined with automated production lines to achieve production automation and intelligence.
3- Application of Resistance Spot Welding in New Energy Vehicles:
In the production of new energy vehicle fuses, resistance spot welding is widely used to connect components such as Fuse Copper Contact, Fuse Copper Cap, Terminal Contact, and Fuse Terminal, ensuring their reliability and safety in high-pressure and high-temperature environments.
Resistance spot welding, as an efficient and reliable metal joining process, plays an important role in the production of new energy vehicle fuses. By accurately controlling welding parameters and quality inspection, it ensures the production of fuses with stable quality and reliable performance, providing guarantee for the safe operation of new energy vehicles
The application of resistance welding in the fuses of new energy vehicles is crucial, especially in connecting components such as Fuse Copper Contact, Fuse Copper Cap, Terminal Contact, and Fuse Terminal. Here is a detailed explanation of the advantages and applications of resistance welding in these metal components:
1. Efficient Connection: Resistance welding provides an efficient method by applying current and pressure between metal components to tightly bond them. This method not only offers fast speed but also enables quick completion of welding, thereby enhancing production efficiency.
2. Reliability: Weld joints produced by resistance welding typically exhibit high strength and reliability. In the fuses of new energy vehicles, maintaining solid connections between contacts, caps, terminal contacts, and terminals is vital to ensure reliable operation under high voltage, temperature, and current conditions.
3. Cost Savings: Compared to traditional welding methods, resistance welding often reduces production costs. Due to its efficiency and reliability, resistance welding minimizes scrap rates and maintenance costs, saving time and money for manufacturers. Wide Applicability: Resistance welding is suitable for connecting various metal materials and shapes, including copper, aluminum, steel, etc. In the fuses of new energy vehicles, where different materials and shapes of metal components are involved, resistance welding offers a flexible and reliable solution.
4. In summary, resistance welding offers numerous advantages in the fuses of new energy vehicles, including efficient connection, high reliability, cost savings, and wide applicability. This makes resistance welding an indispensable and essential process in the manufacturing of new energy vehicles.