PRODUCTS DESCRIPTION
The EV fuse nickel-plated copper cap is an essential element found within electric vehicle fuses, enabling seamless connectivity between the fuse and circuit board or other electronic components. Meticulously crafted from premium-grade copper material and fortified with a protective layer of nickel plating, this product boasts heightened corrosion resistance and conductivity. Its core purpose lies in promptly halting the current flow during instances of overload or short-circuiting, effectively safeguarding electrical equipment and preempting potential accidents, such as fire hazards.
PRODUCT MATERIAL
· Copper stands as a premier conductor, renowned for its exceptional electrical and thermal conductivity characteristics. Its proficiency in efficiently transmitting current while swiftly dissipating heat renders it an optimal selection for a myriad of applications. Within the realm of constructing electric vehicle fuse caps, the utilization of copper material underscores the component's steadfast stability and reliability, even amidst high-current scenarios.
· Nickel plating serves as a pivotal surface treatment method applied to copper surfaces, culminating in the formation of a protective nickel layer. This plating technique augments the corrosion resistance, surface texture, and mechanical attributes of the copper material. By prolonging the product's longevity and enhancing its visual appeal, nickel plating substantially enhances the overall quality of electric vehicle fuse caps. Specifically, within the domain of EV fuse nickel-plated copper caps, nickel plating adeptly shields the copper material from the perils of oxidation and corrosion, thereby upholding its superior electrical conductivity and connection stability.
· Within the domain of electrical connection components like EV fuse nickel-plated copper caps, stringent purity benchmarks are imperative to ensure optimal conductive functionality and steadfast stability. Predominantly, high-purity electrolytic copper emerges as the material par excellence, boasting a copper content exceeding 99.9%. This elevated level of purity guarantees exemplary performance and reliability, adeptly satisfying the rigorous demands of contemporary electric vehicle systems.
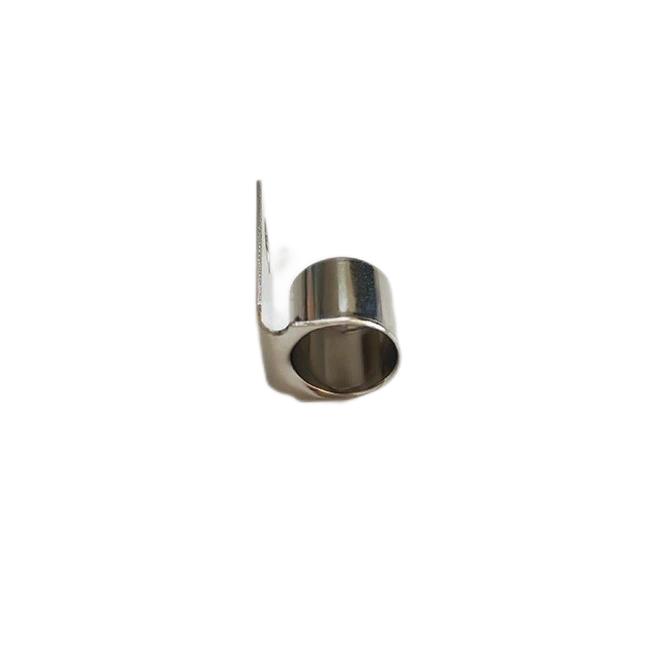
PRODUCT PROCESS
· We start our production process by carefully selecting high-quality copper materials from trusted suppliers, with priority given to high-purity electrolytic copper. At the same time, we obtain the nickel materials and other necessary auxiliary supplies required for the subsequent nickel plating stage.
· The obtained copper material is subjected to precise cutting procedures according to predetermined design specifications to produce copper sheets of precise size and shape. Utilizing advanced technology, we ensure precise molding of copper sheets.
· Next, through meticulous stamping, molding and other precision processes, we strictly adhere to the size and shape requirements provided by our customers to ensure the best product quality.
· During the manufacturing process of nickel-plated copper caps for fuses, welding plays a key role in joining the various components. Utilizing tin-based soldering technology, we achieve a strong connection with excellent electrical performance. Before welding, component surfaces are rigorously cleaned to eliminate contaminants such as oil, oxides, and impurities to ensure the integrity of the welded joint.
· After welding, the surface of the nickel-plated copper cap of the electric vehicle fuse is nickel-plated to enhance its corrosion resistance and conductivity. This critical step is usually performed in specialized nickel plating facilities, using electroplating or electroless plating methods to deposit an elastic nickel layer on the copper surface, thus increasing its ability to resist environmental factors.
· The nickel-plated copper cover is carefully cleaned and inspected, then carefully packaged using shock-proof and moisture-proof materials to prevent potential damage during shipping. These finished products are then safely stored in our warehouse before shipment.
SURFACE TREATMENT
Electroplating treatment: Electroplating treatment is a common surface treatment method that enhances the surface properties of the copper cap by plating a layer of metal or alloy on the surface. Common plating materials include zinc, chromium, nickel, etc. Different plating materials can provide different properties, such as corrosion resistance, hardness and appearance quality.
· Silver plating:
· Bright tin plating:
· Lead-free fog tin plating:
· Nickel plating
Oxidation treatment: Oxidation treatment is a surface treatment method that exposes the surface of the copper cap to oxidizing gas to form an oxide film. This oxide film can increase the surface hardness and wear resistance of the copper cap, while improving its anti-oxidation performance and extending its service life.
Polishing treatment: Polishing treatment is a surface treatment method that polishes the surface of the copper cap to make it smooth, flat, with good gloss and appearance quality. This treatment is often used to improve the aesthetics and decorative effect of copper caps, making them more attractive.
Chemical cleaning: Chemical cleaning is a common surface treatment method that uses chemical solutions or cleaners to remove oil, dirt, and other impurities from the surface of copper caps. This ensures a clean surface and provides a good foundation for subsequent surface treatment processes.
Anti-oxidation treatment: Anti-oxidation treatment can prevent oxidation and corrosion by forming a protective film on the surface of the copper cap. This treatment method can improve the weather resistance and stability of the copper cap and extend its service life.
Spray coating: Spray coating can increase the surface hardness, wear resistance and corrosion resistance of the copper cap by spraying a special coating on the surface. This method is often used for specific applications that provide special protection for copper caps or enhance their surface properties.
Frosting treatment: Frosting treatment is a common surface treatment method. By frosting the surface of the copper cap, it can increase its surface roughness and improve its adhesion and wear resistance. This treatment method is usually used where surface texture needs to be enhanced and appearance quality improved.
Anti-rust coating: This treatment method prevents oxidation and corrosion on the surface of the copper cap by applying a layer of anti-rust coating on the surface of the copper cap. Anti-rust coating is usually a special chemical coating that provides an extra layer of protection and enhances the weather resistance and corrosion resistance of copper caps.