PRODUCT PROFILE
LiFePO battery pack aluminum housing is an ideal choice for battery packaging due to its light weight, high thermal conductivity and excellent corrosion resistance. This housing is manufactured using precision machining technology to ensure dimensional accuracy and structural stability. The high electromagnetic shielding effectiveness of aluminum materials also makes it the first choice for protecting batteries from electromagnetic interference.
PRODUCT MATERIAL
Aluminum Alloy Material
The aluminum alloy materials commonly used in LiFePO battery pack housing are 3003 aluminum-manganese alloy, which is widely used due to its excellent formability, corrosion resistance, strength and hardness. 3003 aluminum alloy has a low density, only 1/3 of steel, providing greater lightweight space, while the thermal conductivity is 5 times that of steel, and the energy absorption per unit weight is 2 times that of steel.
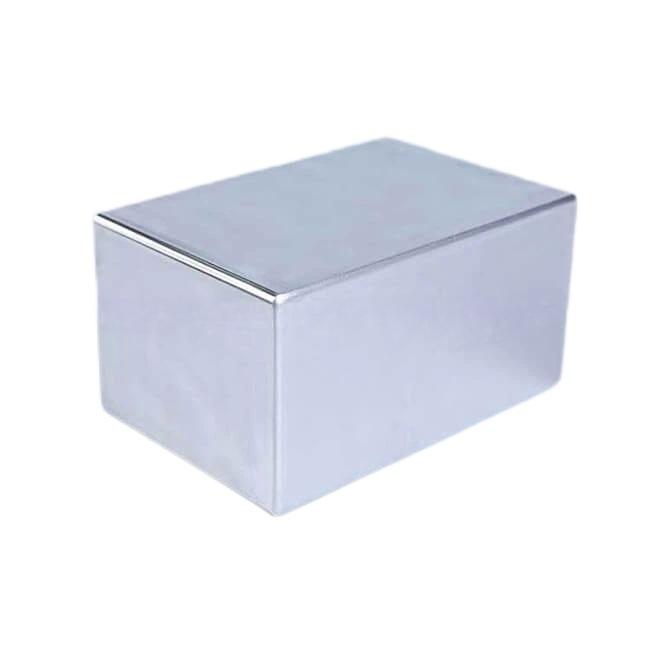
PRODUCT PROCESS
Material preparation: Select suitable aluminum alloy materials, such as 3003 aluminum-manganese alloy, and unwind and discharge the materials to ensure the flatness of the materials and prepare for stamping.
Mold design: According to the technical requirements of the battery shell, design the mold of the continuous punching die, including the stamping shape and size of each workstation.
Pre-stretching of punching sheets: In a large-tonnage punching machine, punching and pre-stretching is performed through continuous dies to form the preliminary shape of the battery shell.
Deep drawing forming: Use a manipulator or automated equipment to perform multiple deep drawing operations in the mold to gradually form the precise shape of the square battery aluminum shell.
Cooling and lubrication: During the stretching process, the mold is equipped with a cooling system to control the temperature, and lubricating stretching oil is sprayed to reduce friction, and improve product molding quality and production efficiency.
Quality inspection: The dimensional accuracy and surface quality of the formed LiFePO battery pack aluminum housing are inspected to ensure that the product meets the design requirements.
Post-processing: Including cleaning, drying, full-size inspection, and appearance inspection, as well as final packaging and boxing, to complete the entire continuous stamping process.
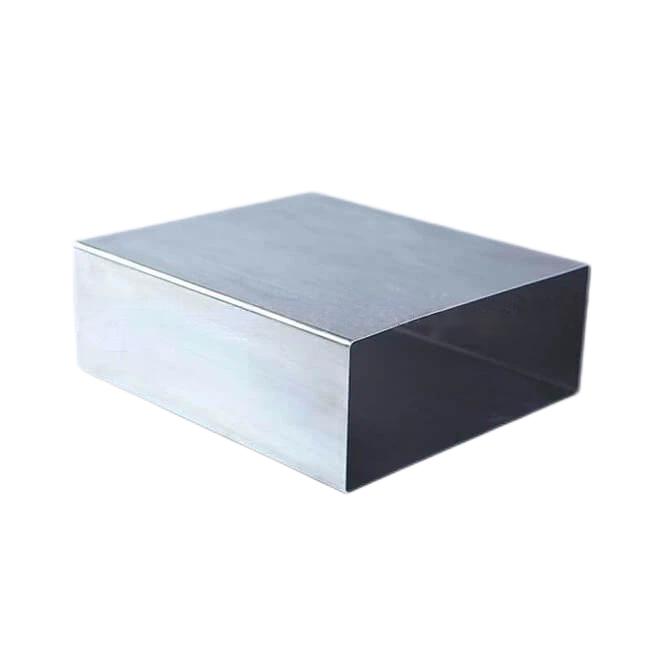
PACKAGING AND TRANSPORTATION
1. Cleaning and Inspection: Before packaging, the aluminum battery casing is thoroughly cleaned to ensure that there is no dust or impurities, and inspected for any damage or defects.
2. Thermoplastic Packaging Bags: The battery casing is initially packaged with thermoplastic packaging bags, which have good sealing and moisture resistance, and can provide additional protection for the battery casing.
3. Pearl Cotton: Inside the thermoplastic packaging bag, pearl cotton is used as a filling material to absorb possible shocks and vibrations. Pearl cotton has excellent cushioning properties and shape plasticity and can provide customized protection for the edges and corners of the battery casing.
4. Fixation and Support: Ensure that the battery casing is fixed and stable in the packaging bag. Additional pearl cotton or other supporting materials can be used to fill the gap to avoid movement or collision during transportation.
5. Carton Packaging: Put the thermoplastic packaging bag together with the pearl cotton into a customized carton. The carton should have good stacking strength and puncture resistance to adapt to different transportation conditions.
6. Sealing and labeling: Use appropriate adhesives or tapes to seal the cartons to ensure that they are not accidentally opened during transportation. Affix clear labels to the outside of the cartons, including product information, weight, dimensions, and indications of fragility or moisture resistance.
7. Stacking and transportation: In the warehouse, stack the packaged LiFePO Battery pack aluminum housing cartons according to safety standards to ensure that the stacking is stable and avoid damage to the bottom cartons due to excessive height. During transportation, follow the correct loading and unloading procedures and avoid rough operations.