PRODUCT PROFILE
The copper metal end cap for the EV fuse is a precision component used for electric vehicle circuit protection. It is made of high-quality copper material and has excellent conductivity and fusing performance. It is suitable for key parts such as battery management systems, motor controllers, onboard chargers, etc. of electric vehicles.
PRODUCT MATERIAL
Material advantages: The selection of high-purity copper material ensures the high conductivity and low resistance characteristics of the fuse copper cap.
Design innovation: The use of advanced design technology ensures that the fuse can quickly cut off the power supply and protect the circuit safety under overload conditions.
High reliability: After strict quality control and testing, it is ensured that the product can work stably under various working conditions.
Strong compatibility: The copper metal end cap for EV fuse is designed with a variety of electric vehicle models in mind and has a wide range of applicability.
Environmental protection and energy saving: Pay attention to environmental protection and reduce energy consumption during the production process, in line with green manufacturing standards.
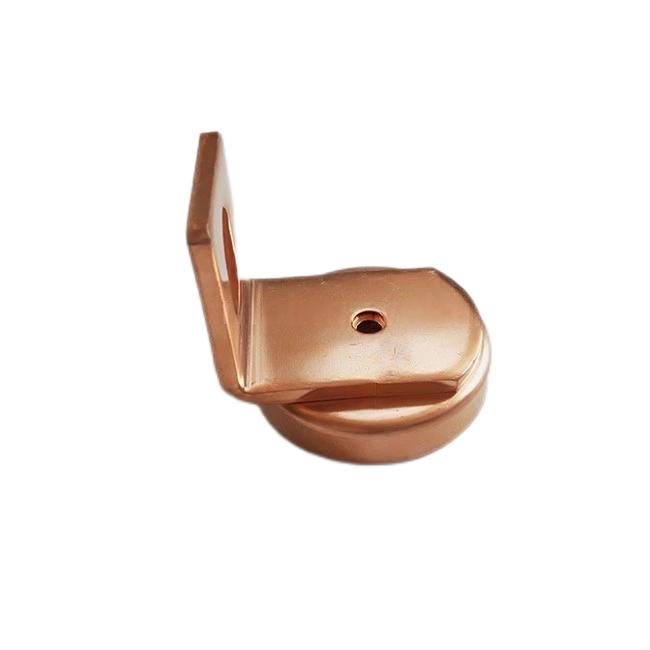
PRODUCT PROCESS
Material selection | Copper material standards: Select high-purity copper materials that meet international standards to ensure that the purity of the material reaches more than 99.9% to provide the best conductivity. |
Physical properties: The copper material should have excellent ductility and toughness to facilitate subsequent processing procedures while ensuring the stability of the fuse under high current. |
Chemical stability: Select copper materials that are not easily oxidized to reduce chemical changes during processing and use, and maintain the long-term performance of the contact knife. |
Precision processing | Cutting: Use a high-precision cutting machine to make preliminary cuts on the copper material to ensure the dimensional accuracy of the contact knife. |
Forming: The copper material is formed into the desired contact knife shape through stamping or casting processes. This step requires precision molds and equipment to ensure the consistency of the shape. |
Polishing: Polish the formed contact blade to remove burrs and surface defects, improve the surface finish of the fuse copper cap, and reduce contact resistance. |
Heat treatment: Perform appropriate heat treatment to improve the microstructure of the copper material and improve its hardness and wear resistance. |
Quality inspection | Dimension inspection: Use precision measuring tools such as calipers and micrometers to inspect the dimensions of the contact blade to ensure that the dimensions meet the design requirements. |
Conductivity test: Use resistance testing instruments to detect the conductivity of the contact blade to ensure that it meets the needs of high current transmission. |
Durability test: Simulate actual use conditions and conduct durability tests on the contact blade, including performance evaluation under environmental conditions such as high temperature and high humidity. |
Fuse performance test: Test the fuse performance of the contact blade under overload conditions to ensure that it can safely fuse within the specified time to protect the circuit. |
Quality control process | Incoming material inspection: Strict quality inspection of all raw materials entering the production line to ensure that the materials meet production standards. |
Process control: Set quality control points in each processing step to monitor the product in real-time to detect and solve problems in a timely manner. |
Finished product inspection: After completing all processing procedures, the product is comprehensively inspected, including appearance, size, performance, and other aspects. |
Traceability system: Establish a complete product traceability system to record the production batch, processing parameters, and other information of each product, so that problems can be quickly located and solved when they occur. |
OUR ADVANTAGES
Packaging material selection
· Internal packaging:
Plastic packaging: Use anti-static and anti-corrosion plastic materials such as polyethylene bags or plastic boxes to protect the copper caps from moisture, dust, and other environmental factors.
· External packaging:
Cartons: Choose sturdy five-layer corrugated cartons to provide additional protection and support. The cartons should have good pressure resistance and impact resistance.
Pallet: For large quantities of copper caps, use pallets for loading to facilitate forklift handling and stacking.
Transportation method
Land transportation: For short-distance or domestic transportation, use trucks or vans for transportation to ensure the stability and safety of the transportation tool.
Air transportation: For international transportation or urgent needs, choose air transportation to shorten transportation time.
Ocean transportation: For large quantities of goods, consider using ocean transportation to reduce transportation costs.