PRODUCTS DESCRIPTION
Bolt-Mounted EV fuse contact is an important electrical component specially designed for electric vehicles. It is mainly used for the connection between fuses and circuits in electrical systems. It is made of high-quality copper material with excellent electrical conductivity and mechanical strength, ensuring stable transmission of current and safe operation of the system.
TECHNICAL PARAMETERS
Material: high purity copper
Surface treatment: tin plating or nickel plating
Working current: in line with customer needs
Operating temperature range: -40°C to 125°C
Size: customized according to customer design requirements
PRODUCT MATERIAL
High conductivity
Made of high-quality copper material, it has extremely high conductivity, which can effectively reduce resistance and energy loss and ensure stable transmission of current.
Strong reliability
Through strict production technology and quality inspection, the performance of each product is guaranteed to be stable and reliable, and in line with industry standards and specifications.
Excellent thermal conductivity
The excellent thermal conductivity of copper material can quickly conduct heat to the surrounding environment, effectively reduce the temperature of the fuse, and improve the stability and safety of the system.
Easy to install
The bolt installation design makes the installation process simple and fast, providing a stable connection and ensuring good electrical contact.
Corrosion resistance
The surface is tin-plated or nickel-plated, which improves the corrosion resistance of the product, extends the service life, and improves the appearance quality.
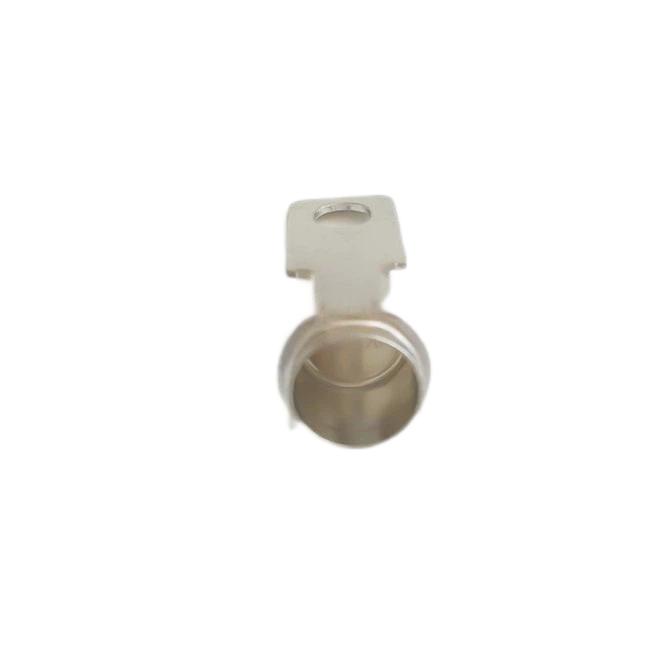
PRODUCT PROCESS
Raw material selection
Purchase high-purity copper materials that meet industry standards, and conduct chemical composition and physical performance tests to ensure that their electrical conductivity and mechanical properties meet the requirements.
Cutting and shaping
· According to the size requirements of the design drawings, precision cutting equipment is used to preliminarily cut the copper plates to ensure that the dimensions of each copper plate are accurate.
· Use shearing or laser cutting technology to finely cut the copper plate to ensure that the edges are smooth and burr-free, and the dimensional accuracy is controlled within ±0.1mm.
Stamping processing
· Using high-precision stamping equipment and special molds, the cut copper plates are stamped and formed into a predetermined structure and shape.
· Molds are maintained and calibrated regularly to ensure dimensional and shape consistency during the stamping process.
Welding assembly
· Using argon arc welding or laser welding technology, the stamped copper sheets are welded and assembled to form a complete copper contact structure.
· Strictly control the welding process parameters, such as current, voltage and welding speed, to ensure the strength and stability of the welding point.
Surface treatment
· Clean the surface of the soldered copper contacts to remove oil dirt and impurities.
· Carry out oxide layer removal treatment to ensure there is no oxide on the surface.
· Carry out tin plating or nickel plating to ensure uniform and smooth coating and improve the corrosion resistance and aesthetics of the product.
Quality inspection
· Use high-precision measuring equipment such as three-dimensional coordinate measuring machines to conduct comprehensive inspections of the size and shape of the product.
· Use equipment such as a microscope to check the smoothness of the product surface and the quality of the welding points to ensure that there are no cracks or burrs.
· Conduct electrical performance testing to ensure that the product's conductivity meets design requirements.
· Conduct environmental tests, such as high and low temperature tests, damp heat tests and salt spray tests, to ensure the stability and reliability of products in different environments.
Packaging and shipping
· Classify and package the products that have passed the inspection, and use shock-proof and moisture-proof packaging materials to ensure that they are not damaged during transportation.
· Develop detailed packaging plans to ensure the safety and convenience of products during transportation and storage.
PRODUCRT APPLICATION
Battery Management System (BMS)
In electric vehicle battery management systems, bolt-mounted fuse contacts are used to protect the battery pack from overloads and short circuits. Its high conductivity and low impedance ensure stable and efficient current transmission in the battery system, providing a safe battery operating environment.
Electric powertrain
The electric power system is the core driving part of electric vehicles, involving components such as motors, electronic controls, and transmissions. Bolt-mounted fuse contacts are used in this system to connect and protect the motor and electronic control unit, prevent current overload and short circuit, and ensure the stable operation of the power system.
Safety and assistance systems
The safety and assistance systems of electric vehicles, such as braking systems, steering systems, air bag systems, etc., rely on reliable electrical connections and protection. Bolt-mounted fuse contacts play an important protective role in these systems, ensuring that electrical faults do not affect the vehicle's safety features.
Vehicle electrical architecture
The electrical architecture of the entire vehicle includes a primary power distribution system and a secondary power distribution system. Bolt-mounted fuse contacts are used to connect and protect the circuits between various electrical modules to ensure the normal operation and reliability of the entire vehicle electrical system.
PRODUCT INSPECTION
We strictly control the production process and quality inspection to ensure that every Bolt-Mounted EV fuse contact shipped from the factory can meet customers' design requirements and standard specifications. In order to achieve this goal, we have adopted a variety of strict inspection methods and technical means to ensure the high quality and reliability of our products. Before the products leave the factory, we conduct random inspections of finished products. Randomly select a certain number of products and conduct comprehensive quality inspections, covering size, appearance, electrical performance and other aspects, to ensure that the quality of each batch of products is consistent.